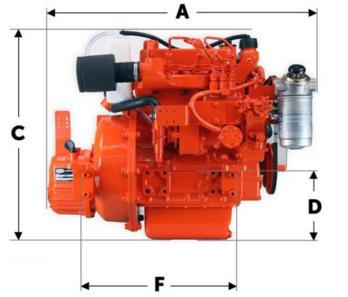
Are you going to install or re-install an inboard engine yourself? Then prepare yourself well, start with the basics and start measuring. Then you can replace an engine with minimal adjustments. For recent engine types, you often know the installation dimensions or they are easy to find. Pay particular attention to:
- propeller shaft height
- engine mounts
- maximum tilt
- reverse gear
- rotation direction of the propeller
- power
- propeller shaft and bearing
In any case, consider what you will need.
Propeller shaft height
First check if the engine matches the propeller shaft height. Are the reverse clutch output and the crankshaft at the same height? If the reverse clutch output is lower than the existing propeller shaft, the engine will ‘rise’.
Engine mounts
On some inboard engines, adjusting the existing engine mounts is not a problem. In case of a steel ship its foundation can be adjusted. In a polyester ship, this is more difficult. Therefore, please check in advance what is possible. Especially with a saildrive, you are often bound to prefabricated through-hulls.
Maximum tilt
Also check whether the inboard engine can handle the maximum tilt when sailing. The maximum tilt can often be found in the manual. A homokinetic drive solves the problem in a different way.
Reverse gear
The Velvet, PRM, Hurth, ZF and Twindisc reverse gears are well known common types. The ratio is often given as engine speed divided by the output speed, e.g. in the ratio of two to one (2:1). This ratio means: Two engine revs / one propeller shaft rev (or simply half).
Often the direction of rotation is indicated with L or R. L 2:1 therefore means: a two-to-one left-hand reverse gear for a left-handed propeller.
You may also come across gears, e.g. for Volvo Penta, with an A for Angle. The axis of these reverse gears is rotated by 7 degrees. Then the motor does not have to tilt as much.
Propeller
Note the direction of rotation of the screw. There are left-hand and right-hand reverse gears. The direction of rotation of the gearbox is determined with the ship moving forward and you looking at the bow.
Be careful with a ‘Z-drive’. The engine will then be reversed, so check the specifications carefully.
AB marine service can carry out the power requirements calculation for your ship.
Power
If you keep the power in the same direction, you can often use the same supply and return connections, such as the exhaust gas outlet, cold water inlet or circulation pipes.
If you are going for larger or smaller power, check the diameter of the connection on the engine. This is already a good indication of the required size.
If the exhaust manifold has a 45 mm diameter, you can use that one. Do not use smaller diameters, this will cause the engine to brake, with all its consequences. Bigger ones are often not a problem.
Propeller shaft and bearing
Also think about connecting the propeller to the reverse gear. Some brands are interchangeable, but this is not always the case. In that case you will need an adapter flange. These are available separately on request or are supplied ready to use with a homokinetic drive.
Want to prevent vibration and save time when connecting? Consider the advantages of a thrust bearing with a homokinetic drive.