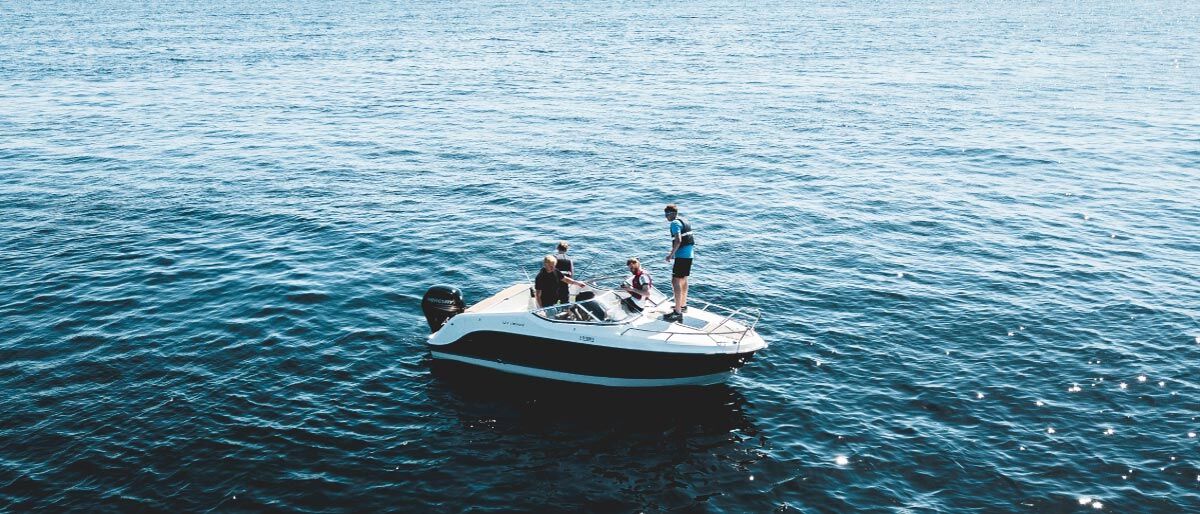
Failures in your engine, collision with a sandbank, a fuel leak… these and other issues cause major problems while sailing and are the nightmare for many a skipper. You can prepare as well as you can, but it is obviously difficult to arm yourself against the unexpected. Do you have quite a bit of technical knowledge and also the necessary tools with you? Heartwarming! But that does not mean you can actually face all issues.
Prevention is hard, cure is not! That’s why you would be very wise to join our partner Vaarzeker to take out a subscription, which ensures you always get the best assistance!
Even if you are not a member, these counsellors may be able to support you. They are just a phone call away from you! Call +31 85 3038253 if you could use some assistance right now. Please note that if you are not a member, you cannot take advantage of free help and there is a good chance you will have to wait longer. Members of Vaarzeker always have priority!
Safety above all
A breakdown is very annoying, but potentially even dangerous! Before calling in Vaarzeker or any other assistance service, it is vital that you are safe yourself first. Especially in case of a fire, leak or power failure. As long as your fellow sailors and you are not at risk, you can plug a leak, put out a fire or switch off the power. In doing so, never expose yourself or others to unnecessary danger, ensure your safety above everything else and call in experts whenever possible!
Subscriptions
As is the case with many services, you are also in a position to decide how much you pay and thus what exactly your options are. That is, you only get assistance with the most important and common problems when you choose the cheapest subscription. With standard or even complete assistance, that package is of course increasingly magnified so that you are carefree on the water! On top of that, the latter two subscriptions offer a 10% discount to boaters who choose to pay per year instead of per month. The three modules are:
Breakdown Assistance
This module includes:
- Call-out charges
- On-board assistance
- Starting aid for battery problems
- Throughout the Netherlands except home port
As long as you are ashore, you can count on the most comprehensive assistance from experienced mechanics thanks to Breakdown Assistance. They do their utmost to get you out on the water the same day. Do you also want technical support while on open water? Then read on quickly!
Assistance Standard
If a technical failure occurs while you are on small inland waterways, your vessel will be towed to a safe port. The Wadden Islands are excluded.
This module includes:
- Call-out
- Towing off
- Telephone assistance for technical questions
- Telephone nautical advice
For a small extra fee, the Breakdown Assistance module is included in this. It is then offered at a 10% discount. Moreover, Assistance Standard is offered throughout the Netherlands, including your home port.
Assistance Complete
Whatever water you find yourself on, you will benefit from a comprehensive assistance package
This module includes:
- Call-out
- Towing off
- Telephone assistance for technical questions
- Telephone nautical advice
- Floating after jamming
- Supply of spare parts
- Fuel delivery
- Towing from port to port
- Removal of objects from propeller
As with Assistance Standard, you can add Breakdown Assistance to this package: in this case, you get a discount of up to 15% on it! Assistance Complete can be used throughout the Netherlands, including your home port.
Carefree boating
When you go out on the water for fun, you always want to be able to count on experts to help you. Got a problem on board? Then you know who you can count on! After making just one phone call, Vaarzeker’s professionals will come to you to solve your problem. Depending on the situation, you can simply sail on to your final destination the same day. Give yourself that peace of mind, become a member and sail for sure.
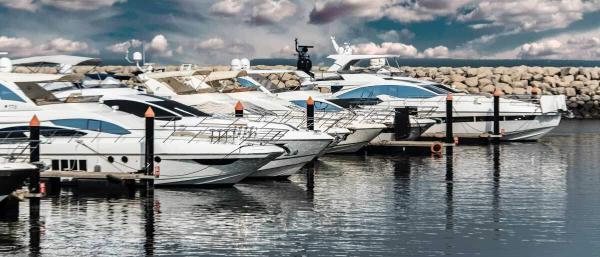