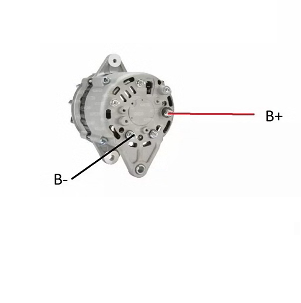
Does the indicator light on your dashboard stay on or does the battery not have the energy to start the engine after a while? Then is it time to replace the alternator of the boat engine.
Follow these 3 steps to replace an alternator yourself
Or go straight to:
- More information about the electrical circuit and circuit testing the installation??
- Alternators: Codes and facts
With conventional dynamos and alternators, one thick cable runs directly from the plus pole of the battery (Terminal B+) or to the distribution point at the starter motor.
After switching on the alternator, a control light on the dashboard indicates whether the circuit is complete. As soon as you turn on the ignition, it starts to light up until the alternator provides counter voltage while it is running. Is there no signal? Then also check the supply up to the contact L or D+ on the alternator.. You can also simply connect it to mass and see if it lights up.
There are also ‘mass-free’ alternators. This means that the whole installation is free from mass (often the engine block). In this case, these cables must also be disconnected.
Often, the alternator’s AC signal is used to drive the rev counter. This is often indicated on the alternator as W-connection. If your rev counter does not work either, this is another indication that something is wrong.
Dismantling the alternator
Switch off the electrical system and disconnect the battery or mass switch. Check that there is indeed no voltage on the cables and that the charging cable runs to the battery (B+) or distribution point. Disconnect the alternator’s electrical wires. Mark the disconnected wires so that you know where to put them again later. Now the alternator is free from the electrical system. Now take it from the engine. In general, it is attached to the front of the engine by means of a clamping and mounting bracket. Accessibility is not always ideal, especially not in a tight engine space, so it may require some creative socket wrench and extension work. Loosen the belt by releasing the tensioning device (1 & 2). Remove the suspension bolt (3).
Buying the right alternator for your boat
On our website you can easily search for the right alternator. The easiest way to find the required alternator is by its number. The number is often printed on a label or engraved on the housing.
You can also search under the category Alternators for the make and type of the marine engine or search by engine type in the search bar. The dimensions and specifications of each starter are shown. The most important measures are in any case dimensions J1 and J2 (in the drawings C and A) and of course the entire suspension design.
At AB Marine service you can buy a (replacement) alternator from:
- Bosch
- Delco Remy
- Denso
- Duccelier
- Femsa
- Hitachi
- Iskra
- Lucas
- Magneti Marelli
- Magneton
- Melroe
- Mitsubishi Motorolla
- Paris Rhone
- SEV
- Valeo
- Visteon
- OEM
See also our video: How to find the right alternator for your boat.
Installing the new alternator
The installation of the new alternator is carried out in reverse order to the steps described above. Make sure that all surfaces are corrosion-free and clean. N.B.: Grease is not conductive. You should therefore always grease the material after installation. This acts a protective layer against moisture penetration. For proper protection between the contacts, use contact spray or conductive paste.
Alternators: Codes and facts
Connecting an alternator is not complicated if you know what the codes mean. In all cases, we are talking here about alternating current dynamos.
Code L or D+: Light on dashboard
In most cases, a ship or boat alternator functions quite simply. A light in the dashboard comes on when you turn the ignition key. If the engine is running, this light will be off again. When the alternator is malfunctioning, you can sometimes see the light burn weakly. This means that the dynamo has low capacity and does not provide sufficient counter-voltage, so that current slowly flows and the light stays on (weakly). If the light does not work, the alternator does not start either. This contact is often referred to as L (Light) or D+ (Dynamo+)
Code IG or R: Always voltage for the alternator
The IG or R contact is a switched wire from the ignition switch. The wire supplies voltage directly to the alternator regulator so that it always receives voltage to switch on.
Simple L and IG connection with T-connector
Code B+, A or 30: Output voltage
An output voltage and current goes from the alternator to the battery. Sometimes there is a diode separator in between to allow two battery packs to be charged separately. You then divide the flow, as it were, into two parts. We usually recommend the use of a battery splitter relay, as it will take less voltage from the charging voltage.
This outgoing voltage wire is often thicker than the other ones and is generally red. It is designated as B+, A or 30.
Minus sign and code G: Mass point
Anything with a minus sign or G for Ground indicates a mass point and can be connected to the motor or minus cable.
Code W: Tachometer or rev counter boat
Then there is the tachometer or rev counter. The alternator generates an alternating current. Each of the coils (usually 3) receives a Hertz signal that is proportional to the number of revolutions. The tachometer converts this signal into an indicated value.
Alternators: Connection codes per brand
All connection codes per brand are indicated in the picture below. American dynamo models often have a completely different coding than the Japanese and German variants. But basically, you will often find the most important and common codes B+ (battery), D+ (light) and W (rev counter).
More information about the electrical circuit and circuit testing the installation?
While sailing, the battery is charged by the alternator on the engine of your vessel. A battery supplies 12 or 24V. If you want more on-board power, choose a larger alternator that delivers more current. In most cases we can supply an alternator with the same dimensions. Get into contact, please send us the current set-up and as much information as possible. Then we will find the right customised alternator for you.